在此次嫦娥三号的研制过程中,新研产品占到了总数的80%,其中任何一个新产品的技术攻关都离不开研制人员的自主创新和反复试验。 在完成这个看似不可能的任务的过程中,研制单位的设计和制造水平都有了重要的突破和跨越式的发展,打出了一张张振奋人心的中国制造牌。 量身打造的着陆腿:强、轻、柔、稳、多、新、全、难 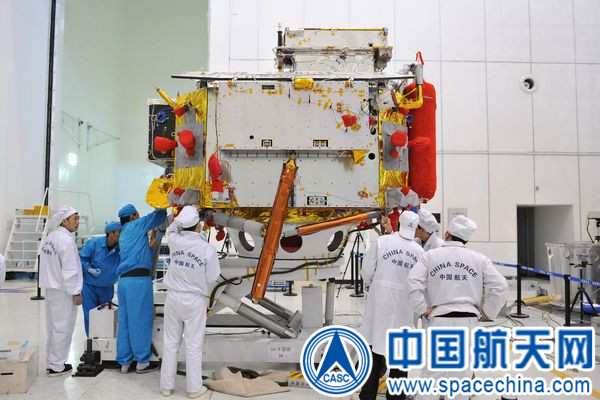
工作人员为嫦娥三号安装着陆腿 在嫦娥三号着陆的过程中,4条着陆腿发挥了至关重要的作用,既承受了竖直和水平方向的压力和冲击力,也保证了着陆器轻柔地、稳稳地落在月面上。而从这个产品的新颖度来说,着陆腿也是我国之前从没有过的航天产品,要达到“强、轻、柔、稳、多、新、全、难”8个方面的要求。 功能重要,却又没有经验可以借鉴,这自然给着陆腿的研制带来了相当大的困难。具体到制造领域,最大的工艺难点便体现在筒类加工上。 嫦娥三号着陆腿主体结构为铝合金管,平均壁厚非常薄,管中填充蜂窝结构,起到缓冲的作用。这段铝合金管精度有多高?从两个指标中就可探知一二。一是尺寸精度,二是形状精度,即在铝管上每一点的测量差值都不能超过头发丝直径的十分之一。 这些指标如果放在一个普通零件的加工上,可能难度并不是很大,但对于一个壁厚薄,加工起来极易变形,而且对长度较大的部件来说,“按照当时的加工能力,这样的精度连想都不敢想。”五院相关工艺师说。 起初,承制工厂的技术人员决定在刚性强、不易变形的钢管上采用分段加工,再进行装配的方法来生产产品。那时是嫦娥三号方案研制阶段,产品只能在工厂精密制造中心一台用了二三十年的老车床上进行加工,尽管车床精度完全无法满足加工精度要求,但车间的工人师傅们靠着多年磨练出的精湛技艺,一点一点试尺寸变化的趋势和误差,通过调床头、校准精度、调整装卡方式等办法,成功制造出满足设计要求的产品。 紧接着,大家继续开展了产品轻量化的技术攻关工作,从机床精度调整、无应力装夹工装设计、应力消除等多方面开展工作,解决了薄壁弱刚性高强铝合金筒类零件的加工难题,生产出了完全满足设计要求的着陆腿主体结构。 其实,着陆腿上每一个部分的材料选择和加工,都经历着新结构、新材料带来的巨大困难。为了寻找既满足设计要求,又性能稳定的缓冲材料,工艺人员试验了大约六七千件不同厂家生产的材料,做了大量的试验来测试其合格率。为了使着陆腿足盆铝制蒙皮的折弯处光滑无褶皱,工艺人员翻资料、做试验,最终采用了一种全新的工艺方法解决了这一难题。这个工艺创新,如今已经在其他的型号上实现了应用。 嫦娥三号着陆腿的制造给工厂的加工水平带来了突飞猛进的进步。目前,工厂精密加工精度已经提升到了微米级,很多当时的技师现在已经成长为高级技师了。随着任务的完成,工艺人员的技术水平和操作人员的技能水平都有大幅度的提高。 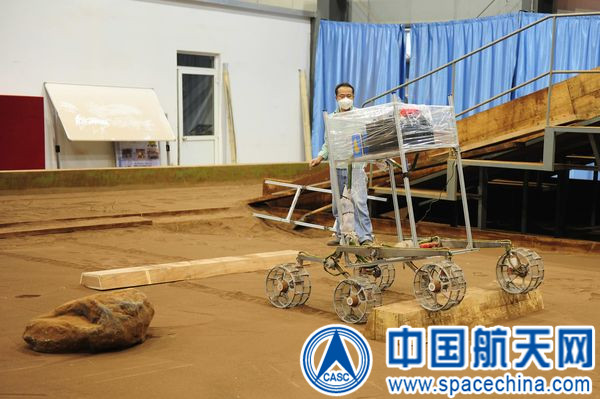
对月球车进行行走试验 镁合金表面处理:从0到1,再从1到10000 在嫦娥三号的研制过程中,“减重”一直是困扰大家的一个重要课题。为了最大化地利用火箭的运载能力,每次转阶段评审会上,都会提出更苛刻的减重需求,甚至会细化到以克为单位。 优化结构设计、把部件壁厚变得更薄……能想到的办法都用上了,还是没办法完全满足重量要求。最后,设计人员决定在嫦娥三号的电子产品机箱结构中采用更轻的镁合金材料,与铝合金材料相比,这将为机箱减重30%左右。 镁合金密度低、比强度高、阻尼减振性好,是航天器理想的结构材料。但镁合金化学性质活泼,硬度低且表面热辐射性能差,平时置放在空气中都会发生腐蚀,极大地制约了其在航天型号产品中应用。因此,攻克镁合金表面处理技术便成为了实现“嫦三”结构轻量化的关键。 简单来说,镁合金表面处理,即在镁合金表面制备一层多功能膜层,从而实现防腐、热控和导电等功能。尽管原理说起来很简单,但因为镁合金化学性质活泼,传统的铝合金表面处理工艺在镁合金上完全不适用,一切都得从零开始慢慢摸索。 “拿化学镀镍技术来说,如果直接把镁合金放进镀液里,会发生剧烈的置换,看起来就像炸丸子一样。”从事热表技术的工艺师介绍道,“这样形成的镀层疏松多孔且与基体结合力差,完全没办法满足工艺要求。” 为了解决这一问题,在镀镍前的镁合金预处理过程中,必须保证将待处理工件表面的油渍、氧化膜、腐蚀产物等多余物去除,裸露出“新鲜”镁合金基体的同时,在其表面生成一层钝化膜,一方面防止镁合金工件暴露在空气中再度氧化,另一方面控制镁合金化学镀镍的起镀速度,从而消除镀层易出现的起皮、起泡等缺陷,提高镀镍层致密性,保证型号产品质量。 为了找到最佳的配方和工艺参数,工艺人员做了上千次试验,一点点调整配方和比例,最终摸索到了合适的工艺方法。“嫦三的研制进度很紧张,我们经常通宵做试验。”研制人员回忆起工艺攻关那1年半的经历,仍然记忆犹新。 在形状简单、体积很小的试验件上的成功,解决了有无的问题,这是从0到1的过程。接下来,一个同样艰难的从1到10000的过程摆在了工艺人员面前,那就是如何将研制结果应用于型号产品中,并且保证稳定的高合格率。 嫦娥三号镁合金机箱形状各异、结构复杂,在鉴定件生产过程中,暴露出了一些问题,合格率不足50%。对此,工艺人员通过不断地分析、试验,逐一解决了这些技术难题。目前,该厂镁合金表面处理产品的一次交验合格率可以达到98%,不论从产品质量还是稳定性方面来说,都处在国内同领域的绝对领先地位。 这场因为嫦娥三号的迫切需求而带来的工艺创新,不仅仅实现了镁合金表面处理技术在型号任务中的成功应用,还在很大程度上带来了制造领域的一次全新突破。 迄今为止,镁合金表面处理技术已成功应用于航天系统内外等单位共计300余套镁合金结构产品的表面处理任务中。随着深空探测技术的发展,保证空间飞行器的轻量化,提高其有效载荷将成为一种大的趋势,因此,镁合金表面处理技术还将拥有更加广泛的应用前景。(江雪莹) 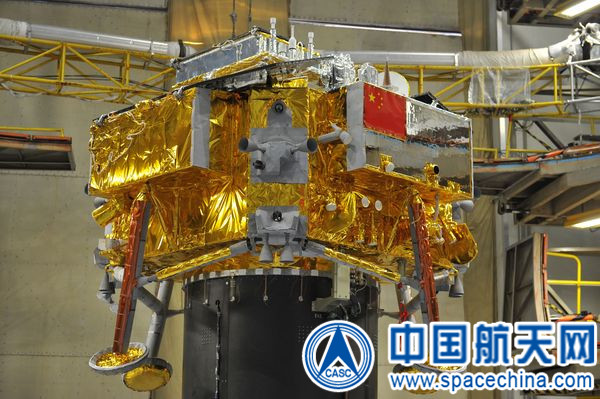
“坐”在火箭上的嫦娥三号探测器 |